Implementation of iCL boosts efficiency at tyrolian firm
“With iCL, we’ve been able to increase our number of inspections per day from 1.5 to 4. Our efficiency has almost tripled, and we now make four new offers per day. Switching to iCL was by far the best decision we’ve made this year.”
Katrin Karbon, Managing Director of Tyrol Fire Safety Centre (Brandschutzzentrum Tirol), Austria
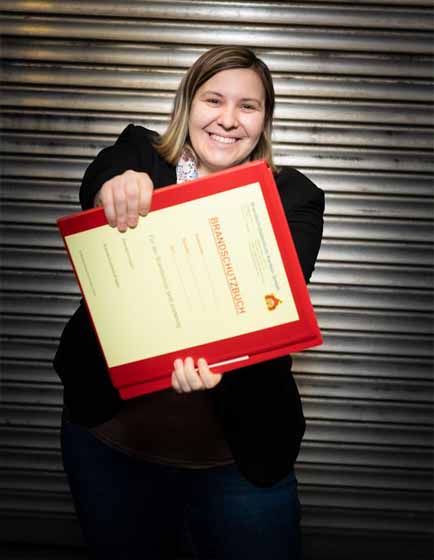
© Martin Vandory
Wanted:
Flexibility and variety
“We’ve realigned our business in recent years to focus on existing buildings. This created a variety of tasks that our previous fire safety solution was unable to map. Our staff were quite dissatisfied with the old solution, and I wanted far more flexibility. I was looking for an electronic checklist we could customise to better accommodate the market and our products,” says Managing Director Katrin Karbon, explaining why they switched to Opti-Q’s fire safety app.
The Tyrol Fire Safety Centre, Austria (Brandschutzzentrum Tirol) works with buildings that have been around for quite a long time. The oldest is more than one hundred years old. Finding a suitable digital solution for these old structures was particularly important to them. Being a full-range supplier, they conduct fire safety inspections, report defects or shortcomings and ensure these defects are corrected.
Found:
An app for everyone
The old solution was far too complicated to use, especially for technicians carrying out fire safety inspections. “By switching to iCL we took a clear step towards the future. Since we have people from different generations working on our team, it was important to me that everyone could work with the app, including the technicians who fix the defects.”
Other people had concerns too, such as Katrin Karbon’s father, the founder and co-managing director of the Tyrol Fire Safety Centre. At first, he couldn’t imagine conducting inspections without a pen and paper. “My father, a court-certified expert, was totally surprised that we had more output with the app and that the office could access the inspection report with just one click,” she says, smiling as she recalls the first time they tested iCL during an inspection.
Implementation:
A leap forward
The company started implementation in spring 2021. Ms Karbon tells us how the switch to iCL played out:
“It didn’t take more than four or five weeks before we inspected the first building. We were totally amazed to get started so quickly. We thought it would take much longer. Implementation was super easy. I’m a construction engineer with no programming knowledge, and it was really simple to understand. What we hadn’t expected at the time was that implementation would be a big ‘aha’ moment for our company. Although we had already been working with a digital solution, we still wrote a lot down. We gradually entered our existing checklists into the Opti-Q solution. When implementing iCL, we checked every procedure. We scrutinised how we work throughout the division and changed and simplified a lot of things. It was a leap forward for our company.”
Where iCL is used:
In every division
The electronic checklist is used in every division of the Tyrol Fire Safety Centre – from inspections to defect recording and processing. Inspectors work with iCL on site during their fire safety inspections. Back in the office, they can get an overview of every defect with one click.
This information is leveraged to send customers new offers. Customer orders are then assigned to the relevant team leaders. The technicians who ultimately fix the defects have the appropriate defects report with them. Even the managing director was surprised to learn that iCL is now being used in every business division: “We thought we would mainly work with the checklist during the inspections and then later in the office to wrap things up. But our staff were so thrilled with the overview functionality that everyone works with iCL now. The iCL dashboard has become a better source of information for us than our own management system. Every employee knows how to use the fire safety app from the get-go and can immediately help customers who phone us up for advice. I use the iCL dashboard myself when I talk to customers because it’s a great sales argument.”
What has changed:
A good feeling and strong growth
The Tyrol Fire Safety Centre manages around 180 properties. Many buildings, such as clinics, have very complex requirements. iCL helps the company stay on top of things at all times. As Katrin Karbon points out, “Since we’ve been using iCL, we’ve seen an increase in inquiries, and we are growing fast. What’s more, everyone on the team feels more at ease when responding to questions from customers.”
Benefit:
Who benefits the most?
“I benefit the most,” says Ms Karbon, laughing. “Because everything’s been running smoothly since we started working with iCL. All our staff benefit, of course, because it’s much easier for them to manage information. Of course our customers benefit too because they get higher quality and better service with their orders.”
Our software solution enables the Tyrol Fire Safety Centre to respond to specific problems. Its managing director Ms Karbon is convinced: “For us, this was by far the best decision we’ve made this year.” She sees a lot of potential for iCL in other areas of the company in future as well.
Opti-Q
Optimising quality with IT solutions
Our team combines IT skills with many years of quality management expertise. This broad knowledge base enables us to develop innovative products and is indispensable when advising our customers.
With iCL, Opti-Q offers a standard software tool for creating complex inspection lists and helps customers integrate IT solutions into their quality management systems.
Opti-Q was founded in 2013 by Paul Zieger, Alexander Marek and partners. When developing software, we collaborate with renowned IT companies, which assist us as we grow and evolve.
Find out how iCL can optimise your company. We look forward to hearing from you.